Pulp Bleaching Processing
Pulp bleaching processing is one of the important pulp making processes, whose purpose is to improve the brightness that is commonly known as whiteness in order to suitable for the different needs. The pulp bleaching processing methods include the delignification and lignin retention bleaching or the oxidation and reduction bleaching. The chemical pulp bleaching processing belongs to the delignification bleaching; the high yield bleaching (Mechanical pulp bleaching) belongs to reduction bleaching or the oxidation-reduction bleaching.
Since the end of 1990s, the elemental chlorine-free (ECF) bleaching and the totally chlorine-free bleaching (TCF) have gotten the rapid developments. The ECF bleaching and the TCF bleaching have been gradually popular instead of the traditional chlorine agent containing bleaching. In the high developed countries in papermaking industry, especially in Northern Europe and North America, they are the pioneers in the use of the oxygen delignification bleaching or other bleaching technologies. Their power is not to affect the production efficiency but reduce the impact on the environment.
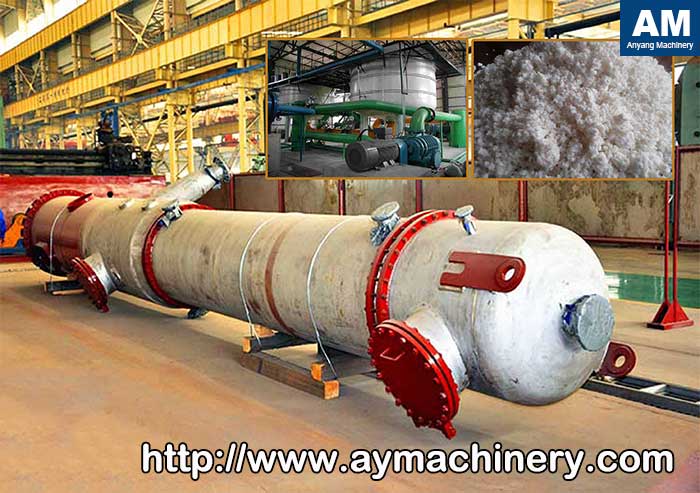
Traditional Pulp Bleaching Processing Technology
The traditional pulp bleaching processing technology includes chlorination, alkali treatment, hypochlorite bleaching, hydrogen peroxide bleaching, oxygen delignification bleaching, ozone bleaching, and sodium hydrosulfite bleaching. After the cooking, the residual lignin in wood pulp is the degradation lignin with high degree of condensation. The part of lignin exists in the form of complex lignin carbohydrate (LCC) residues. The purpose of the chlorination and alkali treatment is to further remove out the pulp residue lignin and lay a good foundation for the subsequent bleaching process. Because the function of the hypochlorite bleaching is low, it is difficult to achieve higher whiteness. Especially in bleaching wastewater containing a lot of carbon trichloride, so it has gradually been replaced by new bleaching agent. Because of the high selectivity of chlorine dioxide in the lignin destruction without significant degradation of cellulose or hemi-cellulose, it can help keep stable whiteness as well as protect the pulp strength well. Therefore, it is widely used in the papermaking industry and has become a key part of all the production process of high whiteness of kraft pulp bleaching processing. Hydrogen peroxide can be used as a bleaching agent for chemical pulp bleaching processing to replace the chlorine dioxide. It can be also as the oxygen delignification additive to improve the effects of the oxygen delignification bleaching.
This successfully opens up a new path for the chlorine-free bleaching. Oxygen delignification is not only to improve the pulp quality, but also to be as the technical measures to reduce the cost of the equipments. Currently in the developed countries almost all the bleaching processes are treated with the oxygen delignification. Ozone is a strong oxidant which can replace chlorine element for the removal of lignin, and also be used to improve the whiteness. Hyposulphite is a typical reduction bleaching agent. At the beginning of 1930s, it was used for bleaching the mechanical pulp, and then waste paper deinking pulp and some subtraction pulps.
New Development of The Pulp Bleaching Processing Technology
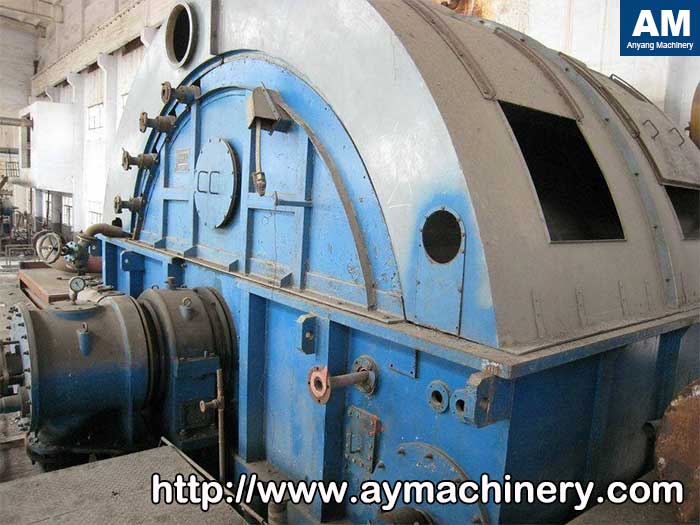
(You may want to learn more about Waste Paper Pulp Production Line)
Two-stage oxygen delignification
The oxygen delignification between the cooking and bleaching stages is considered to be the most effective method of removing residual lignin in the pulp. Further, it is an indispensable part of the TCF bleaching. It is also a crucial part of the most of the ECF bleaching processes. Due to the instability of the oxygen delignification, generally the single-stage oxygen delignification should not exceed 50% in the rate, otherwise it will cause serious degradation of carbohydrates. In order to improve the delignification rate and improve the selectivity of delignification, at present more and more pulp plants adopt the two-stage oxygen delignification.
Biobleaching
In 1986 at the international pulp and paper industry biological technology seminar, the scientist named Viikari from Finland initially reported that people can use bio enzyme to make the pretreatment of pine and birch kraft pulp, which can improve their performance, reduce the chlorine dosage and increase the whiteness of the pulp. Two main types of bio enzymes are used in the pulp bleaching processing. They are Hemi-cellulose and Ligninase. People can use white-rot fungus directly to bleach the pulp, too.
The hydrogen peroxide bleaching with high temperature and pressure
The hydrogen peroxide bleaching or the delignification bleaching are usually limited to 80℃ in the process, because the high temperature is prone to cause hydrogen peroxide decomposition and then decrease chemicals efficiency and chemical pulp strength. This will result in the economic losses. However, as we know, hydrogen peroxide is a weak oxidizing agent, in order to do the TCF bleaching together with obtaining the higher pulp whiteness, we must strengthen the peroxide bleaching process, that is, adopt higher temperature to bleach under higher pressure (usually oxygen pressure) bleaching to enhance the ability of delignification and bleaching effects.
At present, many plants do the hydrogen peroxide bleaching by higher oxygen pressure. At the PO stage, the advantages of both the alkali-oxygen bleaching and the hydrogen peroxide bleaching can improve the bleaching effects. Koukkari and the other scientists apply the thermodynamics and kinetics of higher pressure hydrogen peroxide to make the research on the physical-chemical methods. The results show that in the range of 95-120℃, with the increase of temperature, the consumption rates of H2O2 and NAOH also increase, and the PH value of the pulp liquor decreases. The pulp whiteness increases, and the Kappa value decreases. In contrast, the viscosity loss of the pulp increases. At any constant temperature, with the increase of the pressure, the kappa value increases slightly, while the whiteness is obviously improved. Increasing the pressure can improve the oxygen solubility and enhance mass transferring situation. In theory, the higher oxygen pressure can prevent adverse reactions arousing from the hydrogen peroxide bleaching.
The chlorine dioxide bleaching with high temperature
In the plants, the kraft pulp bleaching processing has now been replaced by the chlorine dioxide bleaching. But usually in chlorine dioxide bleaching, at the temperature between 40-60℃, the main reason of AOX production is the hypochlorous acid (HCL). So the control of PH curve can reduce the maximum amount of AOX production, while improve the chlorine of CIO2 delignification. The study by Lachenal, etc shows that the chlorine dioxide bleaching on the delignification at the high temperature (95℃) can get more effective than that at low temperature (45℃).
Peroxyacid bleaching
Since 1990s, the peracetic acid (Pa), the peroxy sulfate (Px) and mixed peroxyacid (Pxa) have been used the in plants for experimental application. But most are used for the TCF bleaching. Compared with oxygen and hydrogen peroxide, as the delignification agent, the peracetic acid is more effective and more selective. Therefore, peroxyacid can be used for the TCF bleaching for high whiteness.
Development Trend of The Pulp Bleaching
The background of ECF/TCF
First, the researches and tests in recent years has shown that: the wastewater and its sludge from bleaching have detected carcinogenic, mutagenic and teratogenic characteristics that can generate the effects of hormone secretion. This can affect children’s growth and development and cause many brain illnesses and acute toxicity of toxic chlorinated dioxins (Diox Ines) whose toxicity is equivalent to 1000 times of the cyanide, and more than 500 times of strychnine. Second, the pulping and bleaching technology has promoted the development of ECF/TCF technology.
In recent years, the plants adopting the ECF/TCF bleaching pulp has doubly increased. Nowadays, there is a new ECF/TCF pulp plant born every month in China. Meanwhile, the consumption of the ECF/TCF pulp exceeds the supply.