Significance and Prospects of Developing Mechanical Pulping
With the increasing demands for the papermaking pulp, it is urgent and vital for us to develop a high yield pulp. At present, the research on high-yield pulp are developing rapidly in the world. APMP pulping technologies such as spruce, pine and non-wood fiber raw materials (For example, kenaf) have been relatively mature.
In recent years, our pulping industry has been developing the hardwood APMP pulping technologies since 2000 and built many new production lines. The output is about 100t/d-500t/d. The equipment and infrastructure investment are higher. In order to make our country's papermaking industry achieve profitable development, XOQMP pulping technology has been introduced after years of research. Here, X stands for the softening treatment, O for hydrogen peroxide, Q for the chelating treatment, M for squeeze and P for bleaching. It has the advantages of high yield, less leachable matters and less water consumption. It means less investment in equipment and infrastructure. At last, its biggest advantage is that the bleaching and pulping processes can be carried on at the same time.
Semi-chemical Mechanical Pulp
The Semi-chemical mechanical pulp is that raw material is processed by chemical light treatment, and then ground into pulp by the mechanical process. Wood is main raw material, and the pulp yield reaches as high as 94%. Common chemical treatment is the alkali process or cooking method under low pressure for a short time. This can only make the fiber material swelled and the structure relaxed. Next, the tearing and grinding processes make it into pulp.
Flow Process of Semi-chemical Mechanical Pulp
The flow process of semi-chemical mechanical pulp mainly includes the procedures of wood peeling and chip cutting of raw materials, screening and washing of wood chips, pre-steaming, chemical adding and saturating, squeezing and tearing, reaction, grinding, latency and pressure grouting.
Peeling of raw material
Wood must be peeled to ensure the quality of the chips. Because the bark in the pulp will bring about a lot of dust and affect the pulp quality.
Chip cutting
Peeled wood shall be cut into 30mm long and 3mm thick of chips along the grain direction. If the waste wood is chosen as raw material, the expected chip is about 60mm in length and 1.2mm-3mm in thickness. The size of chip is suitable for pulp making. The oversized chips and have the impact on quality in the pulp production eventually.
Screening
Wood chips must be screened to remove sawdust and the oversized chips. The oversized chips shall be sent back to the cutter by the conveyor to further get into pieces. Sawdust and bark will be burnt together.
Washing
Wood chips from the preparation system shall be sent to the washing machine. In order to achieve better washing effects, the chips will be agitated in the washing machine to remove surface debris, sand, stone gravel, metals and other impurities. After washed, the chips will be sent to the first section of the pre-steaming tank.
Pre-steaming
As the washed wood chips enter into the steaming tank, the temperature shall be appropriate. The wood chips shall stay here for a few minutes to discharge the air in the chips, helping to reduce the load on the mechanical machine.
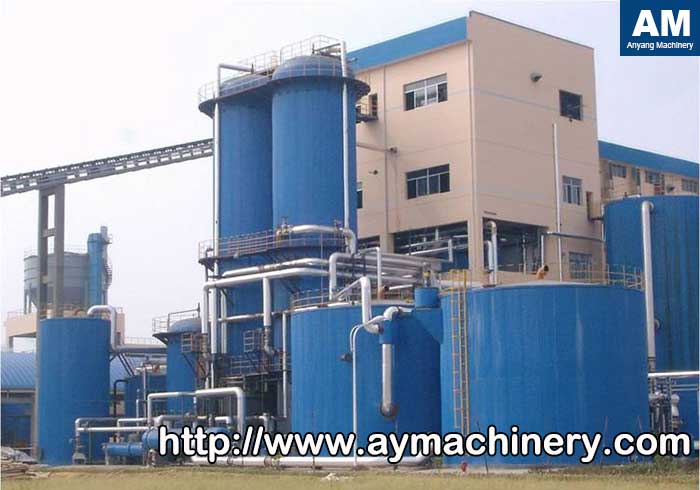
Chemical adding and saturating
It is conducive to soften wood chips on mechanical compression and saturating by adding the chemicals in the tank.
Squeezing and tearing
The pre-steamed chips will be fed into a squeezing and tearing machine by a screw conveyor. The equipment is the key part for XOQMP pulp making. The compression ratio is 3:20. The dryness can reach about 50%. This can squeeze out the air and excess moisture as well as part of the resin. The squeezed wood chips will be changed into wood fiber. Loose wood fiber can absorb as much liquor as possible. The liquor is mainly composed of alkali and hydrogen peroxide and peroxide.
Reaction
The wood fiber shall be sent to the reaction chamber by the screw conveyor and stay here for about 30 minutes. At this moment, the temperature must be proper, and wood pulp and liquor will react fully. After the reaction, the wood fiber will enter the first disc refiner for grinding.
Grinding
The procedure is mainly to use an atmospheric grinding method. Pressure grinding machine may make the internal temperature rise and affect the pulp quality. The grinding concentration is generally about 30%. After the grinding process, the pulp will add white water for dilution. General concentration is about 6%. At last, the pulp will go into the latency pool until the temperature reaches the fiber requirement. The concentration is about 3%, this will last for about 30nim or so.
Washing and screening
Screening shall use 15mm screen to reach refinery selection. Good pulp will be concentrated by the filter press and then enter the pulp tank for papermaking.