With the rapid development of the world economy, common papers such as toilet paper and tissue paper have become indispensable fast-moving consumer goods in daily life. The special function papers such as paper towels and kitchen papers have gradually entered the ordinary family. The increase in demand for tissue paper in the market has also led to continuous optimization of the pulping method in the pulp and paper manufacturing process.
In view of the expanding paper market demand, in order to speed up the continuous optimization of pulping method in pulp and paper manufacturing process, many pulp and paper mills have invested in advanced pulping equipment such as multi-disc vacuum pulp filter and vacuum drum pulp washer, so as to continuously improve the production scale of domestic paper manufacturers. However, there are also many pulp and paper mills, which are facing high production costs, unstable quality, lack of market competitiveness and other problems.
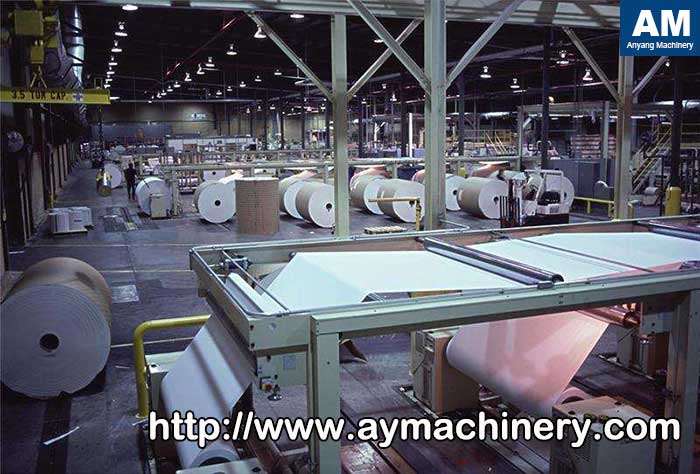
In the future, when the main paper pulping equipment, basic technology and raw materials are basically similar, to produce high-quality and more functional household paper, more efforts should be made in raw materials, process research and development, production management and equipment optimization. The requirements of sustainable economic development and the increasingly fierce market competition pressure have forced paper manufacturers to improve the speed of paper machines, tap potential energy conservation and emission reduction, and reduce pulp consumption, water consumption, power consumption and steam consumption. It can be seen that technological innovation and process optimization are increasingly important in the competition of the paper industry. In order to further reduce the energy consumption of a production line and improve the quality of life paper, we have made useful research and production practices on how to optimize the pulping method in the pulp and paper manufacturing process, and achieved remarkable energy-saving results.
Pulping condition before optimization
Raw material: 100% wood pulp
Long fiber, bleached sulfate coniferous wood pulp (NBKP)35%;
Short fiber, bleached sulphate broad-leaved wood pulp (LBKP)65%.
Pulping method before optimization
The long and short fibers are mixed and beaten by a double-cone refiner (DCR) after being mixed with a certain ratio of pulp, and then mixed with the disintegrated damaged pulp, and finally into a slurry tank by a double-disk refiner (DDR).
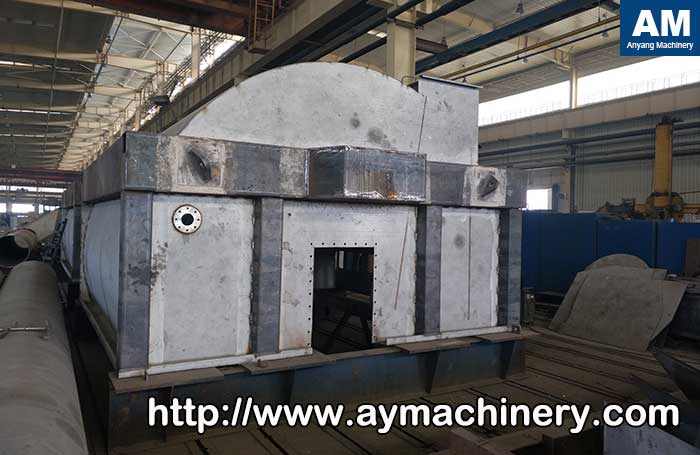
Problems need to be optimized during the pulp and paper manufacturing process
Binding force
The strength of paper mainly depends on the binding force of fiber, and grinding is the most effective method to improve the binding force of fiber. The original long and short fiber mixed pulping process, double cone refiner (DCR) has high running load and long time. In particular, LBKP wood pulp is beaten twice by DCR and DDR, which intensifies the transverse cutting of LBKP short fibers and affects the paper strength.
Tooth break
Double disc refiner (DDR) original grinding disc is prone to broken teeth and zigzag wear, has a short service life, and will break the pressure screen drum when passing through the pressure screen due to the falling of the tooth into the slurry system. Through the pressure screen drum tooth piece directly into the flow pulp box, will crush the vacuum circular screen paper machine special stainless steel forming network, serious damage blankets, seriously affect the normal production order, to the production cost, operation stability and paper quality and other aspects of a lot of trouble.
Excessive pulping
Due to the low paper strength, the operating power of DDR is generally adjusted according to the physical strength condition of 20KW or more, which can improve the strength of paper forming, and basically meet the standard, but some pulps are excessively beaten, and several unfavorable phenomena will occur.
- Sawtooth wear of the grinding blade leads to a decrease in the grinding area, and the grinding power needs to be increased to reach the predetermined beating index, which leads to an increase in fiber cutting, and a significant decrease in the thickness of the pines into paper. The wrinkling rate needs to be increased to improve the softness of the paper into paper, which affects the efficiency of the paper machine.
- The amount of steam in the dryer should be increased, mainly because the drying capacity of the web is insufficient under the same conditions after the refining power is increased.
- The increase of fine fibers is manifested in the fact that the paper machine guide rollers are more stalked, the washing is frequent, and the air-floating white water treatment is more difficult.